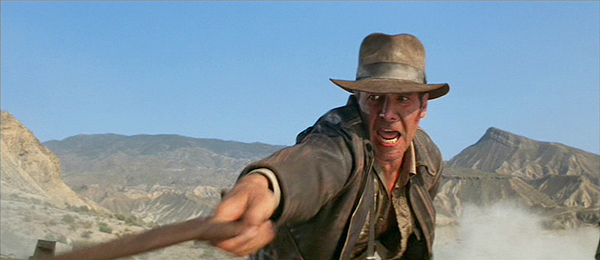
Indiana Jones is undoubtedly one of the most iconic film characters of the 20th century. Known as the whip-cracking archaeologist, the bullwhip is one of his most visible signature items. This section features those whips, including information on many of the bullwhips actually used in the film series. It also contains commentary, reference material and provides an expansive link covering the various commonly asked topics regarding the bullwhips used in the four Indiana Jones films.
“We had a guy come to my house for a couple of lessons with the bullwhip in the beginning, I think it was three or four lessons. Then it was up to me to practice with it and get it right. If anybody could explain it in words, I’m sure it would be a lot easier to do. It’s a combination of relaxation while snapping the wrist at the proper time. It’s really all a matter of timing. Once you’ve learned how to do it, you remember the basics so you’re not lashing yourself with the whip. I usually practice with several bullwhips on posts and trees. It’s not an easy thing to learn, though. I did take the bullwhip out a few weeks before I started on Indy III and loosened up a bit.”—Harrison Ford
Whipmaker David Morgan is credited with making the bullwhips used in the Indiana Jones Films.
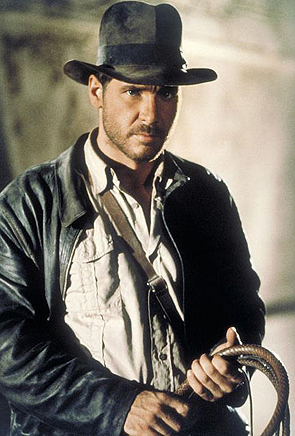

“While the story gave great scope for the use of the whip, it never became a distraction. Rather it became a recognized part of the Indiana Jones character and an ongoing factor maintaining the suspense of the story. The superb use of the whip in developing the story lines in these movies undoubtedly contributed to their success.” —David Morgan (pg. 102 Whips and Whipmaking, 2nd Edition)
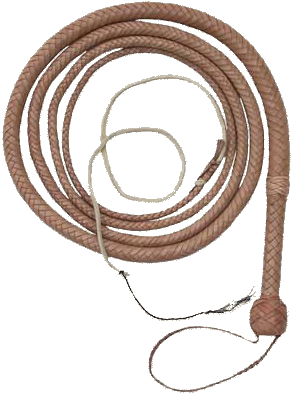
The 450 series bullwhips were used in the Indiana Jones movies
“This whip, as the No. 453 8 ft. length or the No. 455 10 ft. length, became an icon when it was so skillfully woven into the story by Glenn Randall, the stunt director for the first movie…Equally as important the association of this whip with these outstanding movies led to a resurgence in interest in whips in movies, stage performances, and in sport whip cracking. There are now large numbers of Indiana Jones fans, many cracking whips.” —David Morgan
David Morgan supplied more than 30 bullwhips of the 450 series for the Indiana Jones movies. They ranged from six feet to 16 feet long. These are moderately heavy bullwhips with the weight carried out well into the thong. The handle foundation is about eight inches long. The whip is well balanced and features a 12-plait natural tan kangaroo hide overlay. The standard length carried in the movies was the No. 455 10-foot bullwhip. The other lengths were used in special stunts. The length is measured from the butt to the end of the braid. It does not including the fall.
Prior to 1974, David Morgan had been importing and supplying bullwhips made in Australia. However, in December of 1974 the United States placed a ban on the import of Kangaroo products when the Red, Western Grey and the Eastern Grey kangaroos were listed as threatened species. This embargo on kangaroo hides and kangaroo products ultimately forced him to start making his own bullwhips using an alternate leather: a very strong and durable leather called kip side, a hide from young cattle.
Construction
“The number 450 series bullwhips, which where used in the Indiana Jones movies were developed as an American style bullwhips using the Australian braided belly construction. The outward style of the whip was taken from and Australian bullwhip which I had been selling to stuntmen for some years. The whip has a wrist loop, a diamond braid on the handle part, and a knot separating the hand part from the four-seam work of the thong.” —David Morgan (pg. 102 Whips and Whipmaking, 2nd Edition)
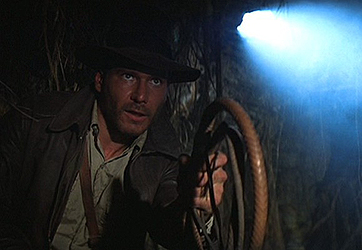
Mr. Morgan’s design went back to the classical heavy, short-handled American style bullwhip, but using the braided belly construction of the best Australian whips. When the embargo on kangaroo products ended in April of 1981 he began to use kangaroo hide exclusively.
Over the years there have been several minor changes in the basic appearance of this whip, however the over all design remained basically the same. The changes have been limited to improvements in the core and shape of the whip. The most noticeable difference between the old whips and the modern ones is in the visual length of the handle. Although the foundation is the same length, the reduced distance between the knots on modern David Morgan bullwhips makes the handle look shorter. Though knot placement has always been a decorative addition to the whip, and and its placement on the handle was considered irrelevant, this was done as an improvement so that the decorative ring knot was not placed directly under the transition zone, a high stress area.
“There are obvious variations among the individual whips, since each kangaroo skin varies and all work from cutting through braiding is done by hand. The overriding priority has been to make the best whip possible in terms of handling characteristics and durability, to be a working bullwhip in the American tradition.” —David Morgan
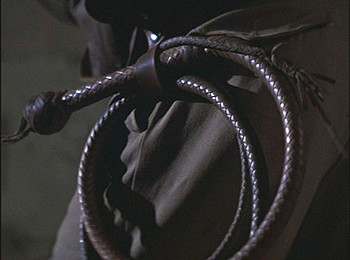
The handle foundation of the David Morgan bullwhip is an 8-inch long a steel spike. It is well loaded with lead tape to add weight and to balance out the moderately heavy thong. These whips are made in layers and have two braided bellies, two bolsters and a 12-plait overlay. The center of the whip consists of twisted leather covered by a filler or bolster. That core is plaited over to form the first belly of the whip. That first belly is then covered by another bolster, which is then plaited over to form the second belly. So in essence you now have one whip built over another whip. That second belly is then covered by another bolster and then the final overly is then plaited around that with the overlay strands cut wider and ending with a 6-strand point for improved durability in use in rough conditions. The bullwhips were also fitted with replaceable Australian style fall on the end to take the brunt of the wear and tear as the whip is used.
“The design established for the 450 series whip was a heavy whip, much like the older cowhide bullwhips, well balanced with a loaded butt, and brought to a point rather finer than the old bullwhips, but coarser then the Australian Stockwhips. The end was finished in and Australian type fall and cracker. The shape or taper was made to suit wraps and the basic movie needs but still work with the Australian type fall for close cutting and target work as well as coarse cutting.
The construction of the thong followed the plaited belly construction of the Australian stock thongs. The first few whips where made using calf or kip, but after the embargo on kangaroo was lifted, only kangaroo was used (except for the fillers and bolsters that where made of kip). In order to have a durable whip capable of resisting the harsh usage often encountered in stunt work the overlay was cut from a heavyweight kangaroo skin and the strands cut wide. The twelve-strand overlay of the Australian whip was maintained since it lent itself to the development of a durable whip. For the first few year, the falls where cut from white hide tanned in England, but the quality of this hide dropped off, and for years the falls where made of an Australian red hide, which was much more reliable. Currently falls are being cut from a high quality Australian white hide.” —David Morgan (pg. 105–106 Whips and Whipmaking, 2nd Edition)
The Color of these bullwhips is natural tan, however the bark tanned leather used in making these bullwhips will darken in time with use and exposure to sunlight. It is believe that some whips may have been dyed a darker brown by the production to give them an older more weathered look, however there is no official evidence of this yet. The poppers/crackers were made from heavy twisted black nylon thread.
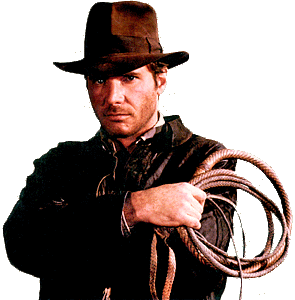
Raiders of the Lost Ark
Bullwhips used in Raiders of the Lost Ark came from stunt coordinator Glenn Randall’s inventory prior to 1981 so it is believe that many of these whips may have been made from Kip side. It is nearly impossible to tell the difference in Kangaroo and Kip with out looking at the cross sections of the leather grain under magnification.
These whips are typically characterized by a slimmer handle and thong. The handle is straight with a slight taper just before the ring knot. The ring knot is located right at the end of the spike. This, along with the thinner handle diameter, gives the Raiders whip its characteristic long handle look.
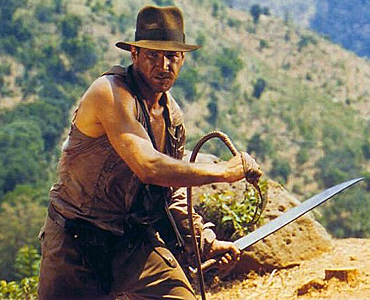
Indiana Jones and the Temple of Doom
It was not until the release of the theatrical trailer of Raiders of the Lost Ark, that David Morgan was approached by Bermans & Nathans and contracted to make the movie bullwhips. He produced 30 to35 bullwhips overall, for the production of The Temple of Doom and later The Last Crusade.
The Temple of Doom bullwhips were made from Kangaroo hide and are typically characterized by a long thin, somewhat tapered handle grip. The decorative ring knot placed at the very end of the steel spike handle foundation giving it the look of a longer handle then subsequent Indiana Jones bullwhips. It is thought that some of the Bullwhips used in Raiders of the Lost Ark, may have ended up being used again in the Temple of Doom. Many of these whips also appear darker then the original natural tan Raiders Bullwhips.
Ford’s proficiency with the bullwhip proved again to be valuable when completing a scene in which he whips a sword from the hand of a Thuggee swordsmen in one take. It was commented by one member of the film crew, that “He (Harrison Ford) could shave George Lucas with that whip”.
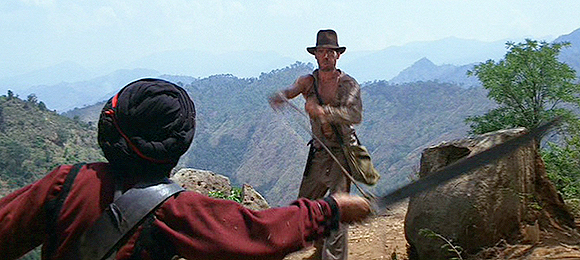
Indiana Jones and the Last Crusade
These bullwhips were again made by David Morgan specifically for the film. Like the Temple of Doom bullwhips, they were made from kangaroo hide. However, these bullwhips typically sport a less tapered and slightly thicker handle then the previous bullwhips. The thong is slightly thicker as well. The ring knot, still located at the end of the spike, was moved slightly lower.
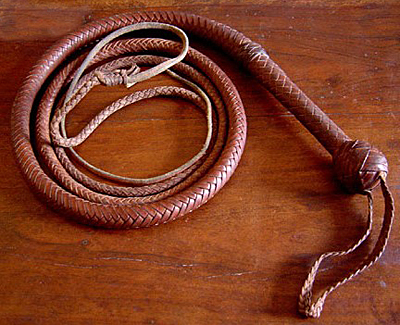
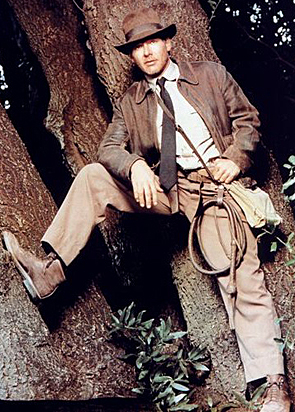
Last Crusade’s Young Indy Bullwhip
During the opening segment Indiana Jones and the Last Crusade, there is a scene in which young Indiana, played by the late River Phoenix, is shown cracking a bullwhip for the first time.
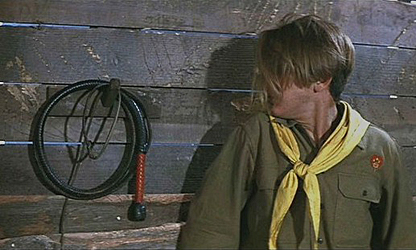
It has been reported that this was a child’s whip made by Swayne, Adney and Brigg’s, However; the design and construction of the bullwhip show it to most likely be one of David Morgan’s series 450 bullwhips, dyed black & red and the wrist loop removed to make it look different for the required scenes. Two whips were used; one 8-foot, which was shown hanging on the train car wall, and a shorter 6-foot bullwhip that was used during the action sequence.
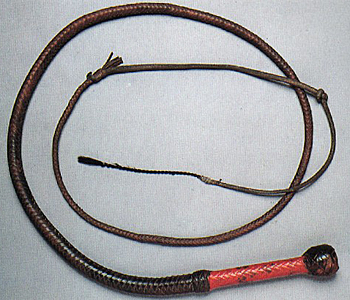
The Adventures of Young Indiana Jones
Two bullwhips were used in the series. Sean Patrick Flannery, playing a young Indiana Jones, briefly used an American swivel handle-style bullwhip in part two of The Young Indiana Jones Chronicles: The Curse of the Jackal/Spring Break Adventure set in March 1916. Young Indiana Jones uses this bullwhip while fighting a grave robbing mercenary named Demetrius, played by Vic Tablian (who was also in Radiers of The Lost Ark playing Barranca & the Cairo Monkey Man).Harrison Ford also carried a bullwhip in his special guest appearance in Young Indiana Jones and the Mystery of the Blues.It is believed that this bullwhip was left over from the previous films.
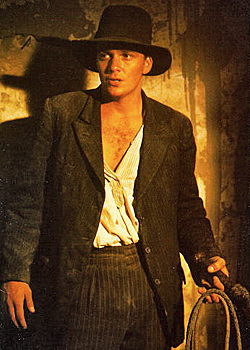
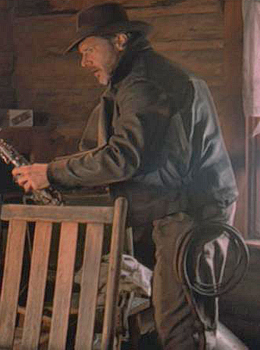
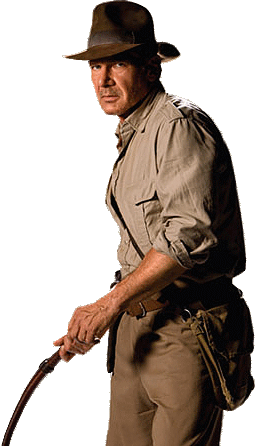
Indiana Jones and the Kingdom of the Crystal Skull
In 2007 Whip maker David Morgan was again contacted to make his series 450 bullwhips in natural tan for the new movie’s production and teaser posters…
“In 2007 we supplied one 453 8 ft. bullwhip and five No. 455 10 ft. bullwhips to Lucasfilm for Harrison Ford’s preproduction training and for the upcoming movie Indiana Jones and the Kingdom of the Crystal Skull. Additionally we provided two special whips; one 12-foot length and one 16-foot length, with either polyester or nylon line running down the center extending 30-feet past the end of the braid. All of the whips were 12-plait natural tan kangaroo hide. Look for our whips when the movie is released on May 22, 2008.” —David Morgan
The film’s bullwhip coach, Anthony Delongis, also brought in several Indiana Jones style bullwhips made by whip maker Terry Jacka to use for filming, his preferred whips to work with.
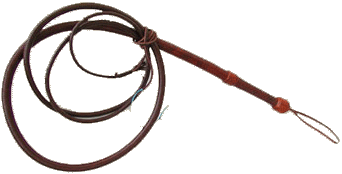
“I have numerous Terry Jacka whips in a variety of lengths, styles and handle dimensions and they always come through for me under the pressures and performance extremes that are the norm in live shows and on horseback where failure isn’t an option. I need to be able to repeat the action effectively and consistently. This is equally true during on-the-set film performances where you’ve got 80 people on salary standing around watching, and you need to get it right in the least amount of time possible. I depend on my own skills and the quality of my equipment to keep my action partners and the surrounding support team safe. I’ve been using Terry’s excellent whips for well over twenty years and I have nothing but praise and admiration for the quality and consistency of his work. He’s my go-to-guy when it’s crunch time and it absolutely, positively has to work.” —Anthony Delongis
Terry Jacka is a seasoned whip maker working out of Queensland Australia and has been a staple in the whip-making world for more than 30 years. His whips have been used in many films including Batman Returns, Wild Bill and The Rundown. He sells many of his products though David Morgan and Western Stage props.
“I learned the fundamentals of whip making and they boiled down to roughly this ‘shape it right and plait it tight’. Quality came from these fundamentals, correct weight distribution and as tightly plaited as the leather would stand. A quality whip was a whip that required the least amount of energy to achieve the required result. This is the goal I have been trying to reach with the design of the bullwhips. The design has been modified over the years, with the introduction of fiberglass as a stronger handle foundation. The handle is a lever and each inch makes a difference to the energy required to work the whip.
(“This “handle is a lever” is a foundation concept to the unique ”rolling loop/follow the handle” style of whip manipulation I’ve evolved over the last 25 years.”) —Anthony De Longis
“Tom (Tom Hill who taught Terry how to make whips ) used greasy chrome split cowhide for the inside workings of his whips and that is the leather I use now. It’s soft, easy to work and has a sponge like ability to soak up plaiting soap. I put the longevity of Tom’s whips down to his use of this leather and its internal oiling ability. I think It is not difficult to plait tightly but difficult to plait a tight bull whip. There is so much leather coming off the handle that you would have to pull the kangaroo set to more than its breaking strain to completely condense the underlying leather. The plaited bellies help but if they are six or four plait as most are then the plaiter would have to be satisfied with the tightness of them because plaiting resists squeezing, and that possibly is as tight as the whip will be.
There was always a small amount of binding on the transition point if the bullwhips we made with Tom, but looking back the whips were more stockwhip like in their action. The things I am trying to do with the binding of the transition is to make a firm base for the set to bite into and won’t stretch or shrink as leather sometimes does, the other is to make the bullwhip a separate animal from a stockwhip. It is not that one is better it’s that both are good for different applications. I use polypropylene twine to try to get the effect of a gradual decrease in the stiffness of the handle. I call this ‘progressive flexibility’, I know its corny but I have to call it something. The bindings are extremely tight and close and go the full length of the plaited belly and overcomes the belly’s resistance to be squeezed. The main bolster and secondary bolster are bound the same way but finish in different positions. Then the foundation is tested for flex and curve and further binding is added depending on the length the whip to be or if I want to adjust the action.” —Terry Jacka
These new bullwhips were made specifically for Indiana Jones 4 and were supplied via the Australian Stock Saddle shop in Malibu, California. They were 10-foot long, short handled versions of Terry’s Australian-style bullwhips done in 12-plait dark brown kangaroo hide overlay with a double plaited belly. The whip is perfectly balanced, with an 8-inch handle similar to the bullwhips David Morgan produced and a handle core that extends three feet into the belly of the whip offering superb accuracy and speed. The kangaroo hide overlay is cut more finely as in the Australian tradition of whip making.
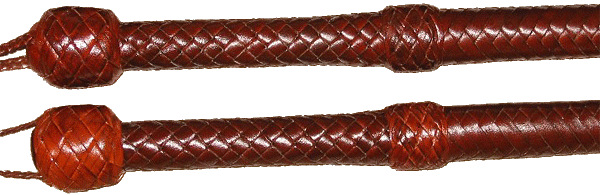
“In June last year (2007) I was asked by Colin Dangaard of The Australian Stock Saddle Co. to supply a couple of unusually styled whips for him. Every now and again Colin asks for something different so I thought nothing of it at the time. Soon after I sent these off the communication from Colin became more often and more urgent, asking for more whips as fast as I could. It seemed almost as soon as a whip was finished a courier was the door to pick it up. All this time Colin was answering my questions by telling me it was all a big secret and he couldn’t tell me anything. Later I was informed that Anthony Delongis was using these whips to train Harrison Ford in whip cracking techniques and that the whips were possibly to be used in the new Indy movie.
The direction I received for the style of the bullwhips was “The same as your 10 inch handled whips but with the handle measuring 5 inches between the turks heads and about a one third larger main turks head.” I sent two eight ft. bullwhips and the rest were ten ft.long. I wasn’t happy to lose the leverage that a 10 inch handle gave me but I made the binding longer and I stiffened the transition at the end of the handle by adding a short tighter bound section and that went a long way in helping to retain the action. All the handles were seven inches long. (8 inches counting the knot) I always finish the bottom turks head (or ring knot) over the end of the handle foundation. The handle length is measured from the end of the whip to the mid point of the second turks head. The handles are about 7/8 inch thick the same as on all my 10ft. bullwhips.” —Terry Jacka
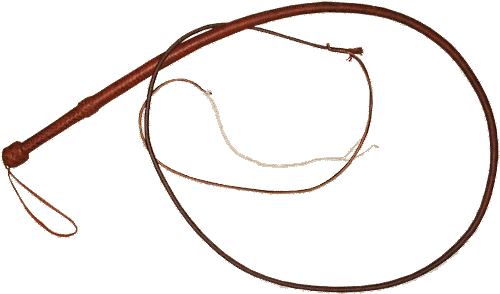
The leather used to on the 12-plait overly was drum stuffed saddle tan kangaroo from Packer Leather, a well-known leather tannery in Australia.
“Drum stuffed means the kangaroo leather has oil forced into the fibers at the factory. This is to help make the leather stronger as far as whip making is concerned and this works fine mostly although I prefer non-drum stuffed if I am able to get the strength I want. Non-drum stuffed holds the color better because the oil in stuffed leather darkens the color; also the whip weighs more because of the oil and tends to kill the action a little. The leather I used on the Indy whips was not heavy as leather goes but heavily oiled and darkened quickly, that is each day there was a noticeable difference in the whips until they reached the color seen in the film.
I use a lot of plaiting soap and with the oil from the leather it sent the whips a darker shade of tan quickly as the kangaroo absorbed the oils from the inside. The turks heads were tied with the same drum stuffed saddle tan. Another batch of drum stuffed leather may not behave the same and that is why I cannot guarantee color. The ten ft. whips weighed about 906 grams average, about 2 lbs. That makes a reasonably heavy whip. About 10% of that weight would be from the heavily drum stuffed leather and I expect most future whips would be lighter. I changed from the usual six-plait point some years ago and made the point thicker and able to take eight plait. This is a different whip to the ones I have been making with its own challenges to overcome to make it as easy to handle as possible.
The falls are American latigo. I switched because the quality in Australian red hide and white hide was not good enough at the time.”—Terry Jacka
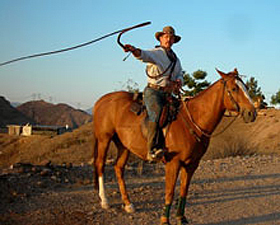

“I asked Terry to copy the dimensions of the Morgan whips that had been made in advance in preparation for some of the planned effects. The design of the “American” style bullwhip, which is the Indy standard, is best suited to single throws from all eight angles of attack on both the forehand and backhand sides. However, this shorter handle makes rapid multiple throws difficult, especially when transitioning from single throws to complex compound combinations, which I wanted to be able to incorporate into Harrison’s whip vocabulary. I knew from my long association with Terry and his methods that he would extend the belly of the whip during construction and give me as tight a weave as humanly possible. While the handle would look almost identical, the stiffer extended belly would provide additional leverage to the help reform the “loop” quickly and facilitate a wider variety of successive throws.” —Anthony De Longis
You can read more about Anthony De Longis and his experience with the Kingdom Of the Crystal Skull in our “Raiders of the Lost Art: Rediscovering the Bullwhip with Anthony De Longis” article.
Some of these screen used bullwhips appear with darker knots this was a result of dyeing. The responsibility of ageing and weathering the whips went to whip coach Anthony De Longis at the request of the films prop master Doug Harlocker.
“Terry’s whip (the one’s that Colin Dangaard arranged) were lighter in color and Doug said the whips needed to look old and worn and to match the colors of the prop whip he had initially given me. I used two coats of a leather dye that Colin gave to me; the one he uses to dye his excellent saddles.
I dyed all the Jacka whips the same so they would look aged at the request Prop Master Doug. I don’t know whether they did any additional dying on set (to darken the knots) or whether just the normal wear and tear and dragging them through the dirt during filming and adding Dubbin to keep them moisturized changed the color slightly. The latter seems most likely.” —Anthony De Longis
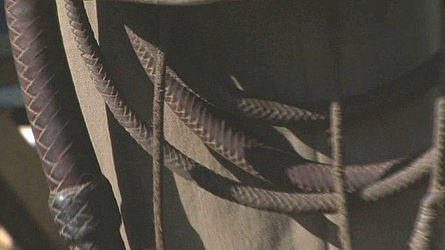
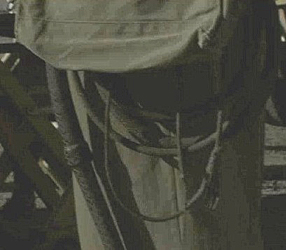
Terry Jacka’s Indiana Jones and the Kingdom of the Crystal Skull bullwhip on the set of the film.
In addition to the whips supplied to the film by David Morgan and Terry Jacka, whip maker Joe Strain also supplied seven of his Indiana Jones style bullwhips to the production of the Kingdom of the Crystal Skull. Joe is a well-known U.S. whip maker, who has been handcrafting whips for more than 18 years. These Indiana Jones style bullwhips were purchased by the film’s production though WesternStageProps.Com and are now exclusively available though Joe’s own company, the Northern Whip Co. His whips have been featured in several other films as well including The Mask of Zorro and the Legend of Zorro.
“This whip is a faithful replica of the whips used in the Indiana Jones movies that we have been producing for over 18 years. We also supplied 7 of these whips to be used in the new production of the Kingdom of the Crystal Skull. This bullwhip is moderately heavy and very well balanced with the weight carried well out into the thong. It has a 12 plait kangaroo overlay with 2 plaited kangaroo bellies, a 8 inch handle foundation and a white hide fall. A hard-hitting whip, the length is measured from the butt of the handle to where the fall is hitched on. Handmade by Joseph Strain and available exclusively from Northern Whip Co.” —Joe Strain
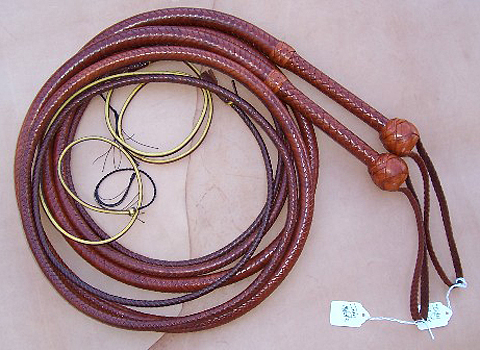
The release of the Kingdom of the Crystal Skull on May 22nd 2008, confirmed that Terry Jacka’s bullwhips where the hero whips carried and used by Harrison Ford in the film. While The original David Morgan Indiana Jones style bullwhips where used in the films first promotional posters in July 2007 (right), it is also believed that the specialty bullwhips supplied by David Morgan where used in the swinging sequence in the opening adventure of the film as he was the only one known to make the necessary safety whips. While Joe Strain did supply bullwhips for the production as well, they did not appear to show up on screen.
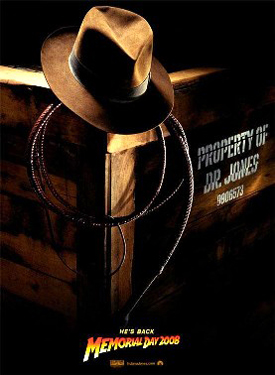
All of his bullwhips supplied for the film were in plaited in saddle tan kangaroo hide. Five of the bullwhips were done in 10-foot length and two were made in an 8-foot length. It is believed that these bullwhips were ordered by the films production to be use for the stunt personal. Six of the bullwhips supplied had the traditional Indiana Jones 5-part 4-bight turkshead handle knot, the type used on the David Morgan bullwhips. One of the 8-foot bullwhips however had the 7-part 6-bight turkshead handle knot which is standard on the Indiana Jones style bullwhips sold though Western Stage Props. These whips were shipped in June 2007. However, The Western Stage Props company sent down at least one 8-foot bullwhip they had in stock at least a month earlier.
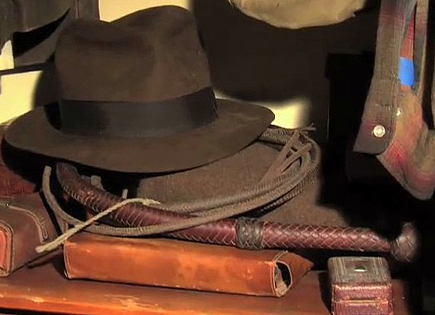